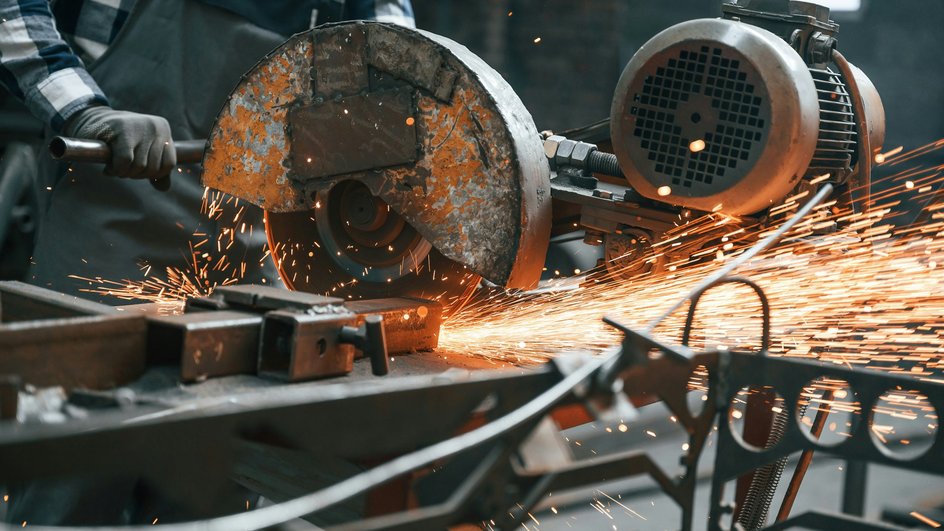
Исследователи ПГУ представили уникальное техническое решение для сборки наразъемных соединений. Это такие детали, которые нельзя разобрать без их полного или частичного разрушения. К ним относятся заклепочные, сварные, клеевые, а также неразъемные соединения, выполненные с натягом. В качестве примера можно привести ось и колесо в железнодорожном транспорте или узлы водопроводных труб.
Главное требование к неразъемным соединениям — прочность крепления. Но в отдельных отраслях, таких как автомобилестроение и авиация, еще важно соблюдать герметичность. В этих случаях применяют соединение с натягом — особый вид соединения деталей, когда диаметр вала больше диаметра втулки. Существует несколько методов их изготовления: прессование, нагрев и охлаждение. У каждого есть свои недостатки. Нагрев требует значительных затрат электроэнергии, что увеличивает расходы производителя и повышает стоимость конечного продукта. Кроме того, процессы нагрева и охлаждения могут быть опасны для работников, увеличивая риск травм.
Команда ПГУ предложила создавать соединения с натягом методом запрессовки. Детали собираются под действием пресса, при этом происходит пластическая деформация выступов, что позволяет заполнять пустоты на поверхности и достигать необходимой прочности соединения. В ходе исследований ученые вывели зависимость, которая позволяет рассчитывать оптимальные параметры выступов, что делает разработку универсальной и применимой к различным материалам. Метод не требует использования клея или герметиков, а это значительно упрощает технологический процесс и снижает себестоимость.

«Будущую герметичность мы закладываем во время изготовления детали, то есть осуществляем формообразование. Мы обеспечим герметичность. И для этого не нужно автоматизации и больших усилий для запрессовки», — яснила старший преподаватель кафедры «Транспортные машины» Юлия Накашидзе.
В ПГУ уже протестировали более 30 образцов из различных металлов и сплавов, которые выдержали давление воздуха в 10 атмосфер — стандарт ГОСТа по герметичности. Сейчас метод уже запатентован и готов к применению в промышленности России.
Ученые ожидают, что в ближайшее время новая технология будет внедрена на пензенском предприятии по производству направляющих втулок блоков цилиндров внутреннего сгорания.
«Наше техническое решение можно использовать в различных отраслях: для производства датчиков измерения, заклепочных соединений, направляющих втулок, гидрораспределителей», — отметил профессор кафедры «Транспортные машины» Николай Курносов.