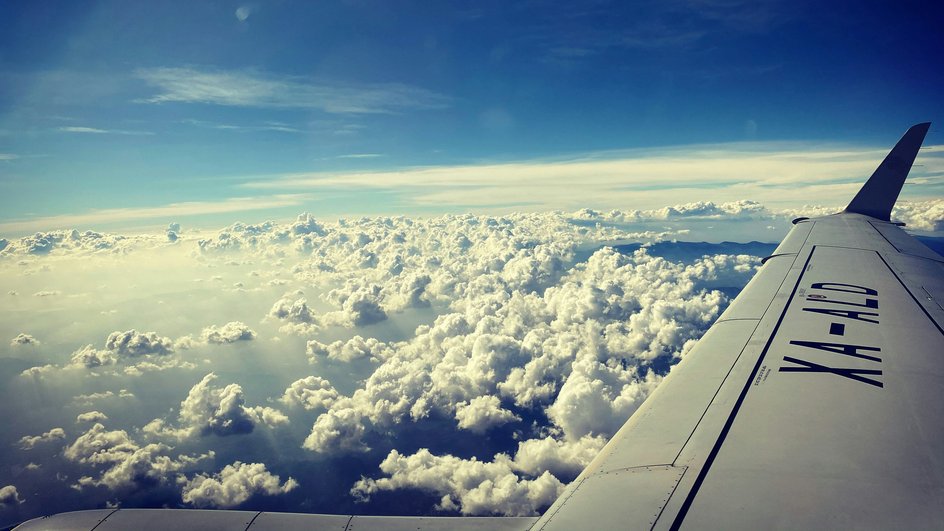
Электроэрозионная обработка — один из основных методов изготовления деталей для авиации, особенно когда речь идет о сложнообрабатываемых материалах. Технология основана на воздействии электрических импульсов, которые испаряют металл, позволяя создавать сложные формы и миниатюрные отверстия. Однако у этого метода есть серьезный недостаток: на поверхности обрабатываемой детали появляется так называемый «белый слой» — зона с измененной структурой, содержащая микротрещины. Этот дефект снижает прочность и долговечность детали, что особенно критично для авиационных двигателей, где каждый элемент работает под колоссальными нагрузками.
Ученые Пермского национального исследовательского политехнического университета (ПНИПУ) предложили решение этой проблемы. Они создали математическую модель, которая позволяет заранее прогнозировать толщину дефектного слоя и количество микротрещин в зависимости от режимов электроэрозионной обработки.
Особенность электроэрозионной обработки в том, что она незаменима при работе с высокопрочными сплавами, где традиционные методы резания неэффективны. Например, при изготовлении лопаток и дисков турбин авиадвигателей требуется исключительная точность и отсутствие дефектов. Однако из-за воздействия электрических разрядов на поверхности металла неизбежно образуется дефектный слой, который может стать причиной преждевременного повреждения детали.
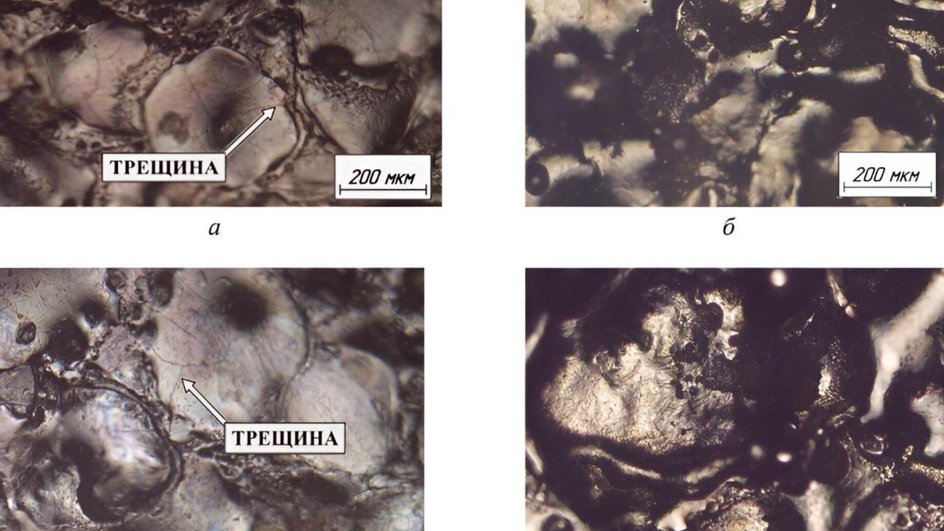
До сих пор не существовало точных методов прогнозирования этих дефектов, что заставляло производителей либо увеличивать запас прочности деталей, либо проводить дополнительные проверки. Ученые ПНИПУ решили эту проблему, создав модель, которая учитывает силу тока, напряжение и длительность импульса. Исследователи протестировали два режима обработки — минимальный (2А, 50В, 40 мкс) и максимальный (8А, 100В, 150 мкс) — на хромосодержащих сталях 40Х и 35ХГС, широко применяющихся в машино- и авиастроении.
Результаты показали высокую точность модели: отклонение расчетных значений от экспериментальных данных составило не более 5%. При минимальных режимах обработки толщина дефектного слоя варьировалась в пределах 20-25 мкм, а при максимальных 55-85 мкм. Количество микротрещин также значительно увеличивалось при более интенсивных режимах.
«Наша модель позволяет заранее определить оптимальные параметры обработки, чтобы минимизировать дефекты, поясняет Тимур Абляз, директор Высшей школы авиационного двигателестроения ПНИПУ. Это особенно важно для деталей, работающих в экстремальных условиях, таких, как лопатки турбин или элементы ракетных двигателей».
Напомним, ранее ученые из Перми также усовершенствовали производство кварцевого стекла, которое занимает особое место среди современных материалов благодаря термостойкости к агрессивным воздействиям.